Porosity in Welding: Identifying Common Issues and Implementing Ideal Practices for Prevention
Porosity in welding is a pervasive concern that commonly goes undetected till it creates significant issues with the stability of welds. In this discussion, we will check out the essential elements contributing to porosity formation, analyze its destructive results on weld performance, and review the ideal methods that can be adopted to decrease porosity incident in welding procedures.
Typical Root Causes Of Porosity
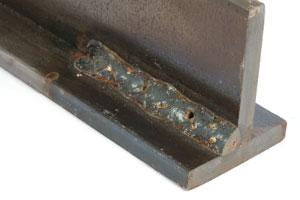
One more constant offender behind porosity is the presence of pollutants externally of the base steel, such as oil, grease, or rust. When these contaminants are not efficiently gotten rid of prior to welding, they can vaporize and come to be trapped in the weld, creating problems. Making use of dirty or damp filler products can present pollutants into the weld, contributing to porosity concerns. To minimize these usual reasons for porosity, thorough cleaning of base steels, proper securing gas selection, and adherence to optimum welding specifications are vital practices in attaining high-grade, porosity-free welds.
Influence of Porosity on Weld Quality

The existence of porosity in welding can dramatically compromise the structural stability and mechanical properties of welded joints. Porosity produces gaps within the weld steel, weakening its overall stamina and load-bearing ability.
Among the primary consequences of porosity is a decrease in the weld's ductility and durability. Welds with high porosity degrees often tend to show lower impact strength and decreased capability to warp plastically prior to fracturing. This can be specifically worrying in applications where the bonded parts are subjected to vibrant or cyclic loading conditions. Furthermore, porosity can hinder the weld's capability to efficiently transfer forces, resulting in premature weld failure and potential safety risks in crucial structures.
Ideal Practices for Porosity Avoidance
To improve the structural integrity and top quality of bonded joints, what details actions can be applied to reduce the incident of porosity during the welding process? Using the right welding strategy for the certain material being welded, such as readjusting the welding angle and weapon setting, can further stop porosity. Regular assessment of welds and instant remediation of any type of concerns identified throughout the welding procedure are necessary techniques to stop porosity and generate top notch welds.
Importance of Appropriate Welding Methods
Applying correct welding methods is extremely important in making certain the structural honesty and quality of bonded joints, building on the foundation of effective porosity avoidance procedures. Welding strategies straight affect the overall strength and longevity of the bonded structure. One essential aspect of correct welding methods is preserving the proper warm input. Too much heat can result in enhanced porosity because of the entrapment of gases in the weld pool. Conversely, inadequate warm might lead to incomplete fusion, developing potential powerlessness in the joint. Furthermore, utilizing the appropriate welding criteria, such as voltage, existing, and take a trip speed, is important for attaining sound welds with minimal porosity.
Furthermore, the option of welding process, whether it be MIG, TIG, or stick welding, ought to align with the particular demands of the project to guarantee optimal outcomes. Correct cleansing and preparation of the base metal, in addition to choosing the ideal filler material, are also vital elements of skilled welding techniques. By sticking to these ideal methods, welders can reduce the risk of porosity development and produce top notch, structurally audio welds.
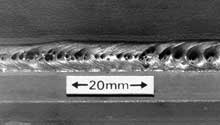
Evaluating and High Quality Control Steps
Quality assurance steps play a vital duty in confirming the integrity and dependability of welded joints. Examining procedures are necessary to find and prevent porosity in welding, making sure the strength you can try these out and toughness view it of the end product. Non-destructive screening methods such as ultrasonic screening, radiographic testing, and visual examination are commonly employed to identify prospective flaws like porosity. These techniques enable for the analysis of weld quality without jeopardizing the stability of the joint. What is Porosity.
Conducting pre-weld and post-weld assessments is likewise critical in keeping high quality control requirements. Pre-weld examinations involve validating the products, tools setups, and sanitation of the workspace to avoid contamination. Post-weld evaluations, on the various other hand, analyze the final weld for any kind of flaws, including porosity, and confirm that it satisfies defined standards. Carrying out a detailed top quality control strategy that consists of extensive screening procedures and inspections is vital to reducing porosity issues and guaranteeing the total high quality of welded joints.
Conclusion
Finally, porosity in welding can be a common problem that impacts the top quality of welds. By determining the usual root causes of porosity and carrying out ideal methods for prevention, such as proper welding strategies and screening actions, welders find out here can make sure excellent quality and reputable welds. It is vital to prioritize prevention methods to lessen the incident of porosity and maintain the integrity of welded structures.
Comments on “Just how to Identify What is Porosity in Welding and Improve Your Strategy”